CASC SERIES COMPACTORS
- Designed for the intermittent processing of wet waste compactors
- Great for Grocery Stores, Retail Stores, Stadiums, and Hospitals
- Fully sealed construction for processing, storage, and transfer
- Faster and more cost-effective than ram style wet waste compactors
- Eliminates the unsanitary build up due to ram drag back
- Odor and pest control with ozone technology
- Optional plug-in dock enclosure for all-weather ease of use
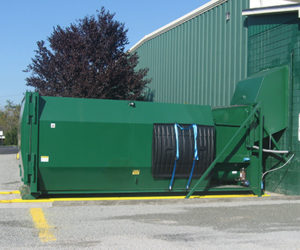

Series Models
The CASC-15 Standard, and the CASC-15 High, denote the height that the auger screw enters the respective unit’s receiving container. The “Standard” model’s screw enters the receiving container lower and is preferable for most ground or dock-fed applications. The “High” model’s screw enters higher in the receiving container providing a larger sump capacity for exceptionally wet waste. A higher screw is also ideal for applications such as dough and other yeast-based products that benefit from top down loading. Each unit is offered with a 10 or 15 horsepower drive, to accommodate available power.
CASC-15 Standard
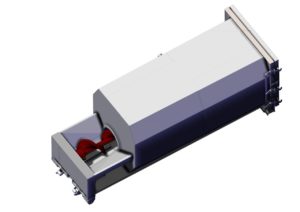
CASC-15 Standard Specifications | |
Chamber Size | 52 x 77” |
Footprint | 270” x 80” x 103” |
Horsepower | 15 |
rpm | 8 |
Weight | 11,140 lbs |
Door | Double Hinged with P-Seal for complete liquid retention |
CASC-15 High
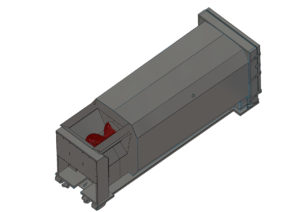
CASC-15 High Specifications | |
Chamber Size | 78.5″ x 76.25″ |
Footprint | 105.9″ x 83″ x 64″ |
Horsepower | 20 |
rpm | 8.85 |
Torque | 11,868 ft-lbs. |
Weight | 12,054 lbs. |
Throughput | 4.14 tons/hr. |
Series Photos
Project Highlight

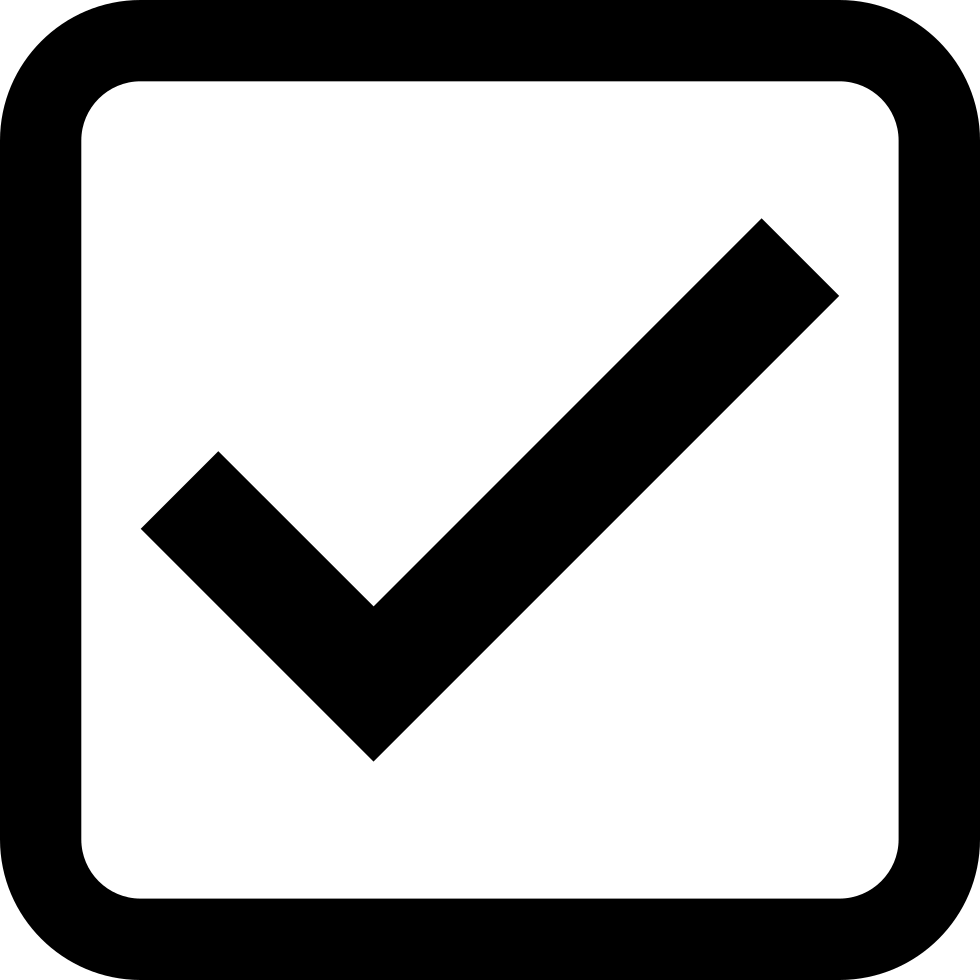
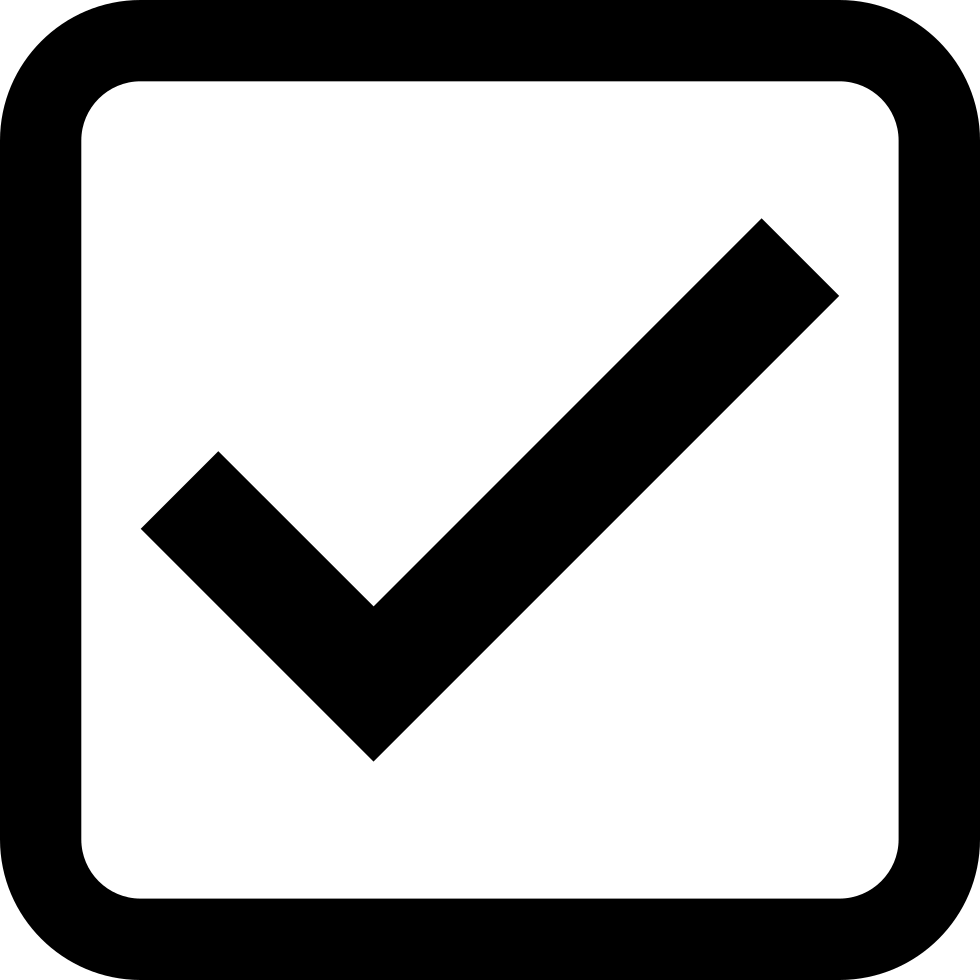
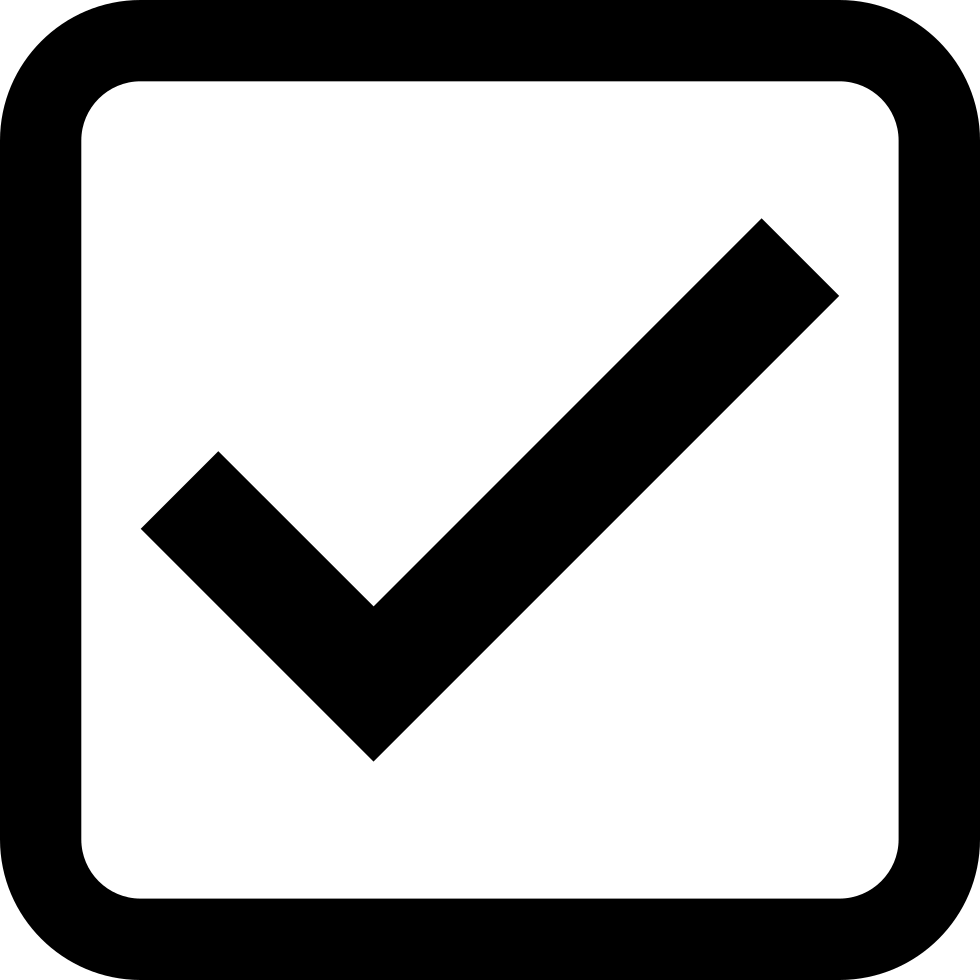
Equipment: CASC-Standard
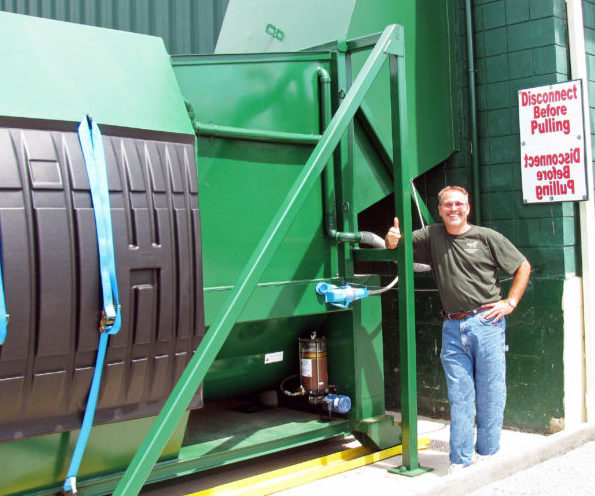